Automotive Plastic Parts: Transforming the Industry with DeepMould
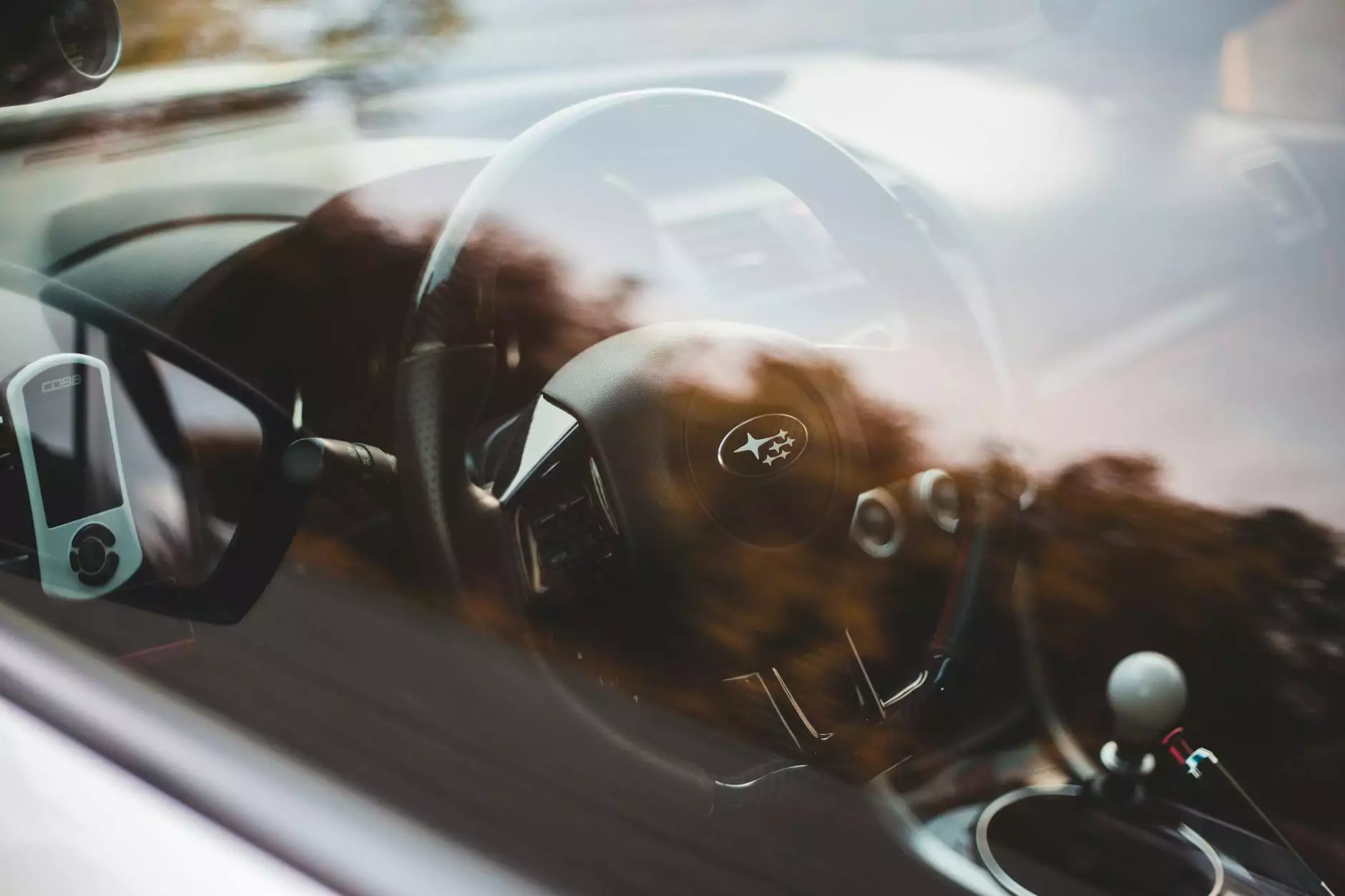
The automotive industry is experiencing a significant transformation, with automotive plastic parts taking center stage as a crucial element in vehicle design and manufacturing. As vehicles evolve to meet modern-day demands, the integration of plastic components is revolutionizing how we perceive durability, weight, and overall performance. In this article, we will delve deep into the world of automotive plastic parts, their advantages, manufacturing processes, and the pivotal role that DeepMould plays in shaping this landscape.
The Rise of Automotive Plastic Parts
In recent years, the shift from traditional materials to automotive plastic parts has been driven by several factors:
- Weight Reduction: Plastics are significantly lighter than metals, allowing manufacturers to produce lighter vehicles that enhance fuel efficiency.
- Cost-Effectiveness: The production of plastic parts often leads to reduced manufacturing costs, which can be passed on to consumers.
- Design Flexibility: Plastics can be molded into complex shapes that would be challenging with metal, enabling innovative designs.
- Corrosion Resistance: Unlike metals, plastics are not susceptible to rust, leading to longer-lasting components.
Understanding Automotive Plastic Parts
Automotive plastic parts encompass a wide range of components used in the construction and assembly of vehicles. These parts can be categorized into various groups, including:
1. Interior Components
Interior components play an essential role in the comfort and aesthetics of a vehicle. Examples include:
- Dashboard Panels: Sophisticated designs can be achieved using high-quality plastics.
- Door Trim: Lightweight yet robust, plastic trims enhance the overall style.
- Seating Systems: Integral parts like seat frames and cushions often utilize plastic for better ergonomics.
2. Exterior Components
The exterior of a vehicle benefits from plastic parts that enhance durability and design. Key components include:
- Bumpers: Made from high-impact-resistant plastics, bumpers are essential for safety.
- Grilles: Plastics allow intricate designs and less weight.
- Fenders: Lightweight and resistant to rust, plastic fenders are a practical choice.
3. Under-the-Hood Components
Under-the-hood parts are critical for vehicle functionality, and plastics are increasingly used for:
- Intake Manifolds: Plastics can withstand high temperatures and various chemical exposures.
- Engine Covers: They enhance aesthetics while reducing weight.
- Fluid Reservoirs: Plastic is ideal for holding fluids due to its non-reactive properties.
Manufacturing Processes of Automotive Plastic Parts
The production of automotive plastic parts involves several innovative processes, each designed to produce high-quality components efficiently. Major methods include:
Injection Molding
Injection molding is the most common manufacturing technique for automotive plastic parts. This process involves:
- Heating: Plastic pellets are heated until they melt.
- Injecting: The molten plastic is injected into a mold cavity.
- Cooling: The plastic cools and solidifies in the desired shape.
Blow Molding
Blow molding is primarily used for creating hollow parts, such as:
- Bottles: Commonly used for fluid reservoirs.
- Fuel Tanks: Offers excellent resistance to chemicals.
Thermoforming
This process involves heating plastic sheets and forming them over molds. It’s commonly used for:
- Dashboards: Allowing for complex shapes and designs.
- Interior Panels: Enhancing the vehicle's aesthetic appeal.
The Benefits of Automotive Plastic Parts
The adoption of automotive plastic parts brings numerous advantages to manufacturers, consumers, and the environment. Key benefits include:
1. Enhanced Fuel Efficiency
Lightweight materials lead to better fuel efficiency, which is increasingly important for consumers aiming to reduce their carbon footprint and save on fuel costs.
2. Lower Production Costs
Plastics often require less energy to process than metals, significantly lowering production costs and, thereby, retail prices.
3. Improved Design Capabilities
Plastic allows for more intricate designs and customization options, appealing to manufacturers looking to enhance brand identity.
4. Sustainability
Many automotive manufacturers are adopting recycled plastics for part production, contributing to a more sustainable automotive industry.
DeepMould’s Role in the Automotive Plastic Parts Industry
As a pioneering company specializing in the production of automotive plastic parts, DeepMould is committed to delivering high-quality components that meet the evolving needs of the automotive sector. Our key offerings include:
1. Custom Manufacturing Solutions
At DeepMould, we pride ourselves on our ability to provide tailored solutions to our clients. We work closely with automotive manufacturers to develop parts that perfectly fit their requirements.
2. Advanced Technology and Innovation
Utilizing state-of-the-art machinery and cutting-edge technology, DeepMould ensures precise manufacturing, reducing waste and maximizing efficiency.
3. Quality Assurance
Quality is paramount at DeepMould. Our rigorous testing and quality control processes guarantee that each part meets industry standards and customer expectations.
4. Commitment to Sustainability
DeepMould is leading the way in sustainable plastic manufacturing, employing recyclable materials in our production processes and minimizing our environmental impact.
Future Trends in Automotive Plastic Parts
The future of automotive plastic parts is bright, with ongoing trends set to shape the industry:
1. Electric and Hybrid Vehicles
The rise of electric vehicles (EVs) and hybrids is expected to increase the demand for lightweight components to enhance energy efficiency.
2. Integration of Smart Technologies
As vehicles become smarter, the integration of electronic components into plastics will become more common, allowing for innovative features and functionalities.
3. Biodegradable Plastics
There is a growing interest in the development of biodegradable plastics, which could further reduce the environmental impact of automotive manufacturing.
Conclusion
In conclusion, automotive plastic parts are revolutionizing the automotive industry, providing numerous advantages in terms of weight reduction, cost efficiency, and design flexibility. Companies like DeepMould play a crucial role in this transformation, offering high-quality, sustainable solutions for modern vehicles. As the industry continues to evolve, the future of automotive plastic parts looks promising, paving the way for innovative designs and technologies.
For more information on how DeepMould can assist in your automotive plastic parts manufacturing needs, visit us at deepmould.net.