The Essential Guide to Plastic Injection Molding for Business Growth
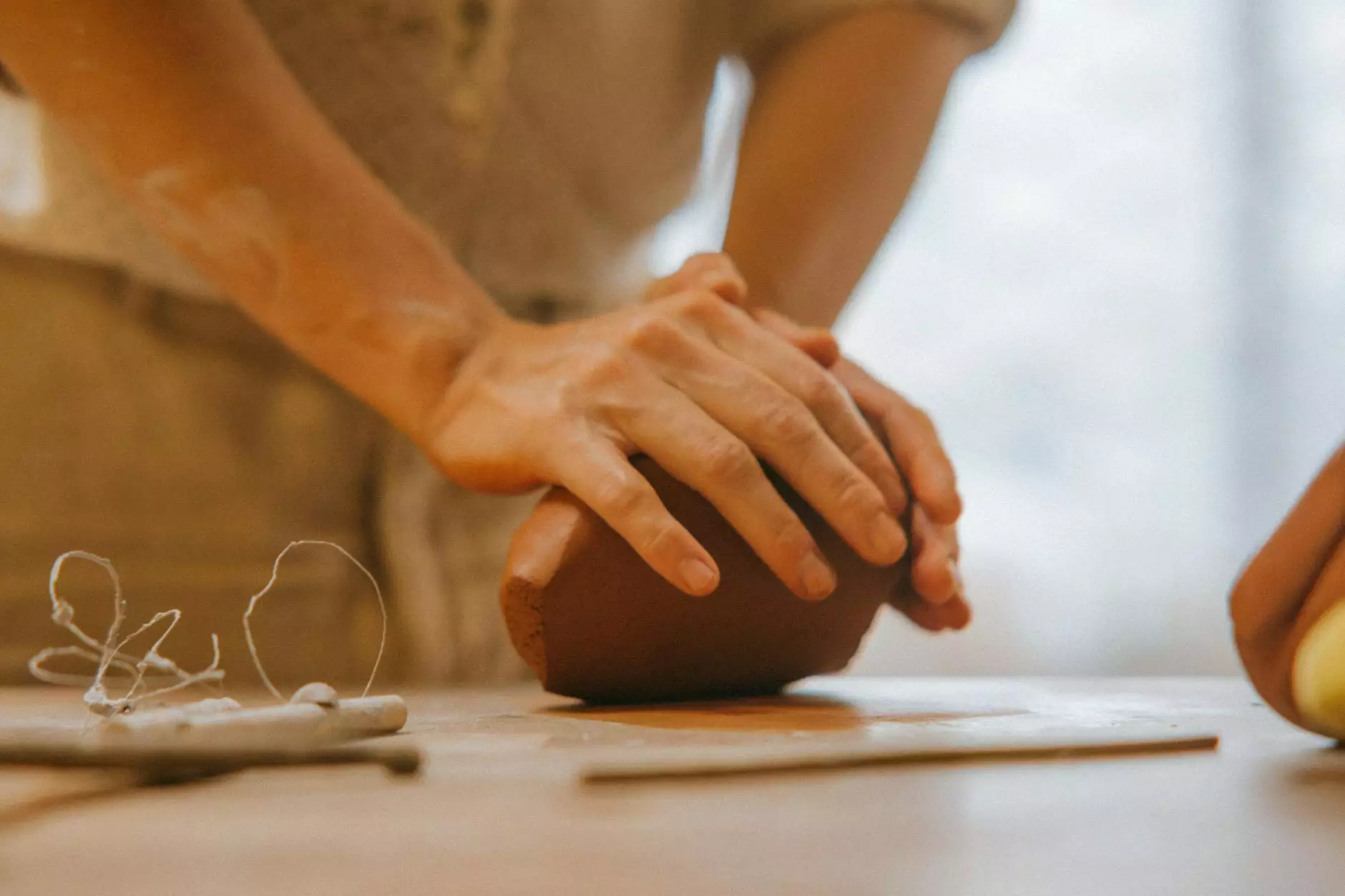
Plastic injection molding has emerged as one of the most efficient and versatile manufacturing processes for creating a variety of products. As businesses continually seek ways to enhance production efficiency and reduce costs, understanding the intricacies of this manufacturing method becomes crucial. In this comprehensive guide, we will explore the benefits of partnering with a professional plastic injection molder, as well as tips on how to choose the right company for your needs.
What is Plastic Injection Molding?
Plastic injection molding is a manufacturing process that involves injecting molten plastic into a mold to create a specific part or product. The process begins with the melting of plastic pellets, which are then injected into a mold cavity under high pressure. Once the plastic cools and solidifies, the mold is opened, and the finished product is ejected. This method is widely used in various industries, including automotive, consumer goods, electronics, and medical devices.
The Benefits of Plastic Injection Molding
- Efficiency: Plastic injection molding provides a high production rate, allowing businesses to manufacture large quantities of products in a relatively short time. This efficiency contributes to lower overall production costs.
- Consistency: The process ensures uniformity in product quality, as each piece is created from the same mold. This reduces the risk of defects and ensures that every part meets the exact specifications required.
- Material Variety: A wide range of thermoplastics and thermosetting materials can be used, offering businesses flexibility in material selection to match product requirements.
- Complex Shapes: Plastic injection molding enables the production of intricate designs and geometries that may not be achievable with other manufacturing methods.
Understanding the Injection Molding Process
To fully appreciate the benefits of plastic injection molding, it's essential to understand the key stages of the process:
1. Designing the Mold
The first step involves creating a precise design of the mold based on the desired final product. This requires collaboration between engineers, designers, and the plastic injection molder to ensure the mold can effectively form the intended shape.
2. Selecting the Material
Choosing the right plastic material plays a critical role in the final product's performance. Factors such as strength, flexibility, and temperature resistance are considered during material selection.
3. Melting the Plastic
The selected plastic pellets are fed into a hopper and then melted in a heated barrel. This process transforms the solid pellets into a molten state, ready for injection.
4. Injecting the Plastic
The molten plastic is injected into the mold cavity using a high-pressure hydraulic system. This step is crucial as it determines the mold’s filling speed and pressure, impacting the final product's integrity.
5. Cooling and Solidification
Once injected, the plastic is allowed to cool and solidify within the mold. The cooling time varies depending on the material and the thickness of the part being produced.
6. Ejecting the Part
After cooling, the mold opens, and the finished product is ejected using ejector pins. The ejected parts are then inspected for quality assurance.
The Role of Metal Fabricators in Plastic Injection Molding
Metal fabricators play a vital role in the plastic injection molding ecosystem. They are responsible for designing and manufacturing the molds used in the injection process. High-quality molds ensure that the production is efficient and that the final products maintain strict quality standards. Businesses looking to leverage plastic injection molding should consider collaborating with experienced metal fabricators who can create durable and precise molds that enhance production capabilities.
Choosing the Right Plastic Injection Molder
When selecting a plastic injection molder, several factors should be taken into account:
- Experience and Reputation: Look for a molder with a proven track record in your industry. Check customer reviews and case studies to understand their capabilities.
- Quality Assurance: Ensure that the molder follows stringent quality control measures. ISO certification or other quality standards can be indicators of a commitment to excellence.
- Technology and Equipment: Evaluate the technology and machinery being used. Advanced equipment can enhance precision and efficiency in production.
- Material Knowledge: The molder should provide guidance on selecting the right materials for your products. Their expertise can help in choosing the most suitable plastic for your application.
- Customer Support: Strong communication and support can significantly impact your project's success. Choose a molder who is responsive and willing to collaborate closely.
Final Thoughts: The Impact of Investing in Plastic Injection Molding
Investing in plastic injection molding can yield significant returns for your business. The process not only enhances production efficiency but also allows for innovation in product design. By collaborating with skilled metal fabricators and professional molders like those at deepmould.net, businesses can streamline their manufacturing processes and equip themselves to meet consumer demands effectively.
The evolving landscape of manufacturing necessitates adapting to new technologies and methodologies. Businesses that embrace plastic injection molding are better positioned to outperform competitors and lead in their respective markets. As you consider the future of your production strategies, let the advantages of plastic injection molding guide your decisions and fuel your success.